Animaquina is a robot Integrated Development Environment (IDE) designed to control and simulate robots directly within Blender. By leveraging Blender’s powerful 3D capabilities, Animaquina provides a versatile and user-friendly platform for robot programming, visualization, and real-time manipulation. The IDE bridges the gap between digital simulations and physical robotic execution, making it a valuable tool for designers, engineers, and educators interested in robotics.
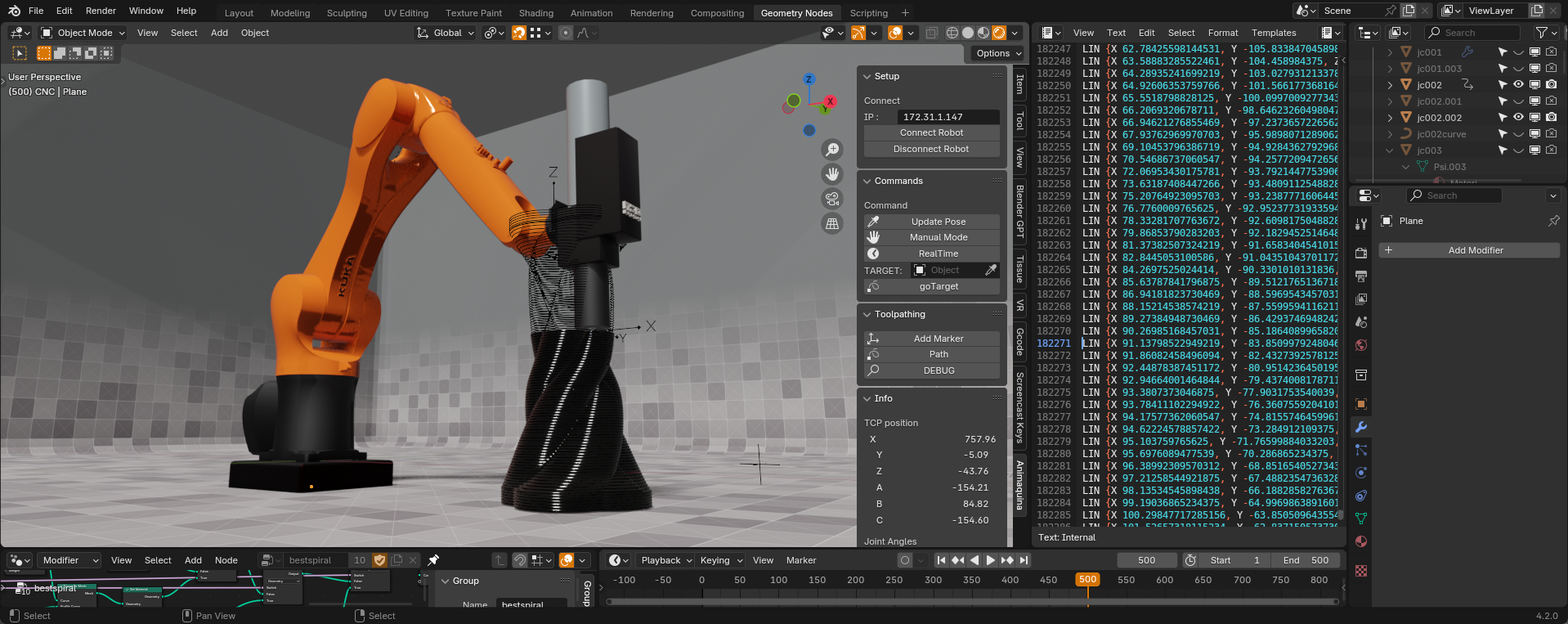
Features
Animaquina offers a range of powerful features, allowing users to intuitively manage robotic simulations and operations:
- IP-based Robot Connection: Connect and control robots over an IP network.
- Real-time Manipulation: Move and adjust robots directly within Blender’s 3D viewport.
- Digital Twin Synchronization: Keep the digital model synchronized with the physical robot.
- Real-time Movement Visualization: Visualize robot movements in real time for immediate feedback.
- Manual Mode: Manipulate the physical robot manually, with real-time updates in the digital twin.
- Marker Placement: Digitize features of the working environment by placing markers in the digital model.
- Toolpath Execution: Create and run toolpaths based on mesh object vertices, useful for complex manufacturing tasks.
- Info Panel: Display the current joint rotation and TCP (Tool Center Point) position.
- VR and XR Integration: Integrates with Freebird XR, allowing for immersive interaction in virtual or extended reality environments.
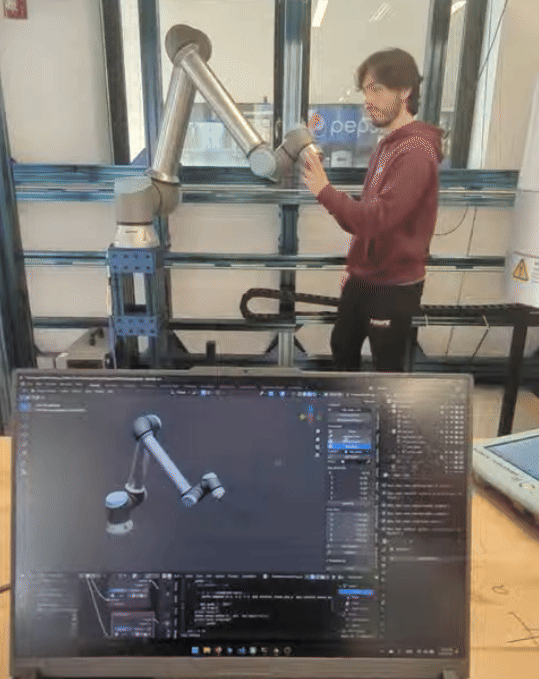
Supported Robot Versions
Animaquina supports different robot models, each optimized for specific platforms:
- Animaquina-UR: Compatible with Universal Robots, tested with models UR5e, UR10e, and UR20.
- Animaquina-Xarm: Compatible with UFactory Xarm robots, tested with the Xarm-6.
- Animaquina-KUKA: Compatible with KUKA robots (limited functionality), tested with KUKA Agilus KR10-1100.
For support or custom integrations, feel free to reach out at: luigi(at)neobrutal(dot)com
.
Applications
Animaquina’s versatility extends to a range of applications across industries:
- Hybrid Manufacturing:
- Develop, manage, and run robotic toolpaths for 3D printing, CNC milling, and more, directly from Blender.
- Art Installations:
- Create interactive art pieces that respond to environmental inputs, choreographed through Blender.
- Theatre and Stage Performances:
- Control moving stage elements, enabling complex choreographies and dynamic performances.
- Education:
- Teach concepts of robotics within an integrated and easy-to-use environment, making learning more interactive.
- Prototyping:
- Quickly test robotic motion in the real world, with direct control from Blender for faster iteration cycles.